1浇口脱料困难在注塑过程中,浇口粘在浇口套内,不易脱出。开模时,制品出现裂纹损伤。此外,操作者必须用铜棒从喷嘴处敲出,使之松动后方可脱模,严重影响生产效率。
1. It is difficult to take off the gate. In the process of injection molding, the gate is stuck in the gate sleeve and is not easy to take off. When opening the mold, the product is cracked and damaged. In addition, the operator must knock out the tip of the copper rod from the nozzle to loosen it before demoulding, which seriously affects the production efficiency.
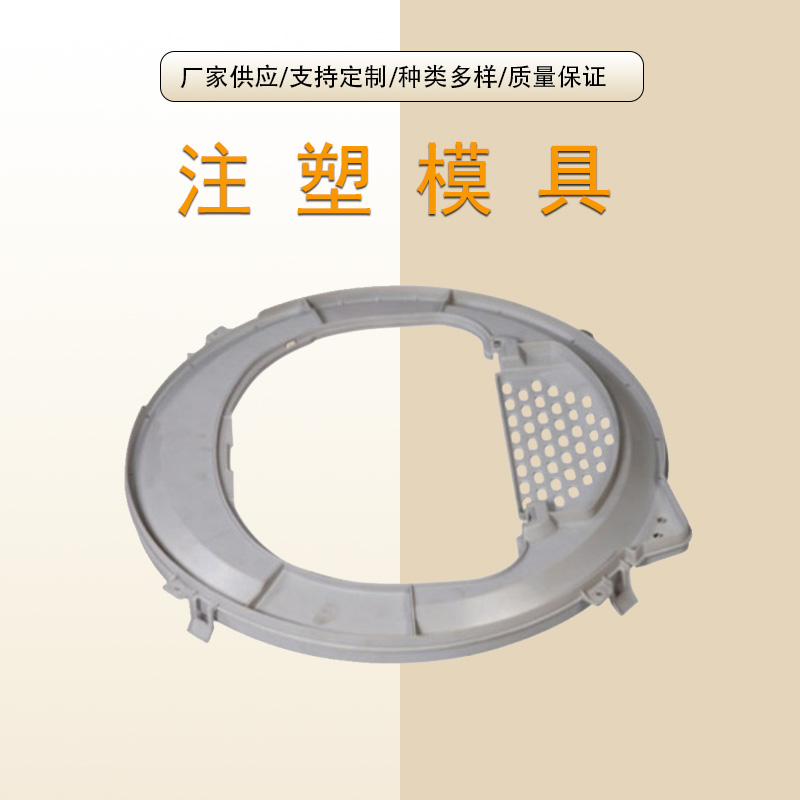
故障主要原因浇口锥孔光洁度差,内孔圆周方向有刀痕。其次是材料太软,使用一段时间后锥孔小端变形或损伤,以及喷嘴球面弧度太小,致使浇口料在此处产生铆头。浇口套的锥孔较难加工,应尽量采用标准件,如需自行加工,也应自制或购买专用铰刀。锥孔需经过研磨Ra0.4以上。此外,必须设置浇口拉料杆或者浇口顶出。
The main cause of the failure is the poor finish of the gate taper hole and the knife mark in the circumferential direction of the inner hole. Secondly, the material is too soft, the small end of the conical hole is deformed or damaged after use for a period of time, and the spherical radian of the nozzle is too small, resulting in the rivet head of the gate material here. The taper hole of gate sleeve is difficult to process, so standard parts shall be used as far as possible. If it needs to be processed by ourselves, special reamers shall also be made or purchased. The taper hole shall be ground to above Ra0.4. In addition, a gate pull rod or gate ejection must be set.
2大型模具动定模偏移大型模具因各向充料速率不同,以及在装模时受模具自重的影响产生动、定模偏移。在上述几种情况下,注射时侧向偏移力将加在导柱上,开模时导柱表面拉毛、损伤,严重时导柱弯曲或切断,甚无法开模。
2 large mold dynamic and fixed mold offset large molds have dynamic and fixed mold offset due to different anisotropic filling rates and the influence of mold self weight during mold loading. In the above cases, the lateral offset force will be added to the guide column during injection, and the surface of the guide column will be roughened and damaged during mold opening. In serious cases, the guide column will be bent or cut off, or even unable to open the mold.
方法为了以上问题,在模具分型面上增设高强度的定位键四面各一个,简便有效的是采用圆柱键。导柱孔与分模面的垂直度关重要,在加工时是采用动、定模对准 位置夹紧后,在镗床上一次镗完,这样可保证动、定模孔的同心度,并使垂直度误差小。此外,导柱及导套的热处理硬度务必达到设计要求。
Solution in order to solve the above problems, a high-strength positioning key is added on the parting surface of the die, one on each side, and the most simple and effective is to use the cylindrical key. The perpendicularity between the guide pillar hole and the parting surface is very important. During processing, the moving and fixed mold are aligned and clamped, and then boring is completed on the boring machine at one time, so as to ensure the concentricity of the moving and fixed mold holes and minimize the perpendicularity error. In addition, the heat treatment hardness of guide post and guide sleeve must meet the design requirements.
3导柱损伤导柱在模具中主要起导向作用,以保证型芯和型腔的成型面在任何情况下互不相碰,不能以导柱作为受力件或定位件用。
3. The guide post is damaged. The guide post mainly plays a guiding role in the die to ensure that the forming surfaces of the core and cavity do not collide with each other under any circumstances. The guide post cannot be used as a stress part or positioning part.
故障主要原因在几种情况下,注射时动、定模将产生巨大的侧向偏移力。塑件壁厚要求不均匀时,料流通过厚壁处速率大,在此处产生较大的压力;塑件侧面不对称,如阶梯形分型面的模具相对的两侧面所受的反压力不相等。
The main reason for the failure is that in several cases, the moving and fixed mold will produce huge lateral offset force during injection. When the wall thickness of plastic parts is required to be uneven, the rate of material flow passing through the thick wall is large, resulting in large pressure here; The side of the plastic part is asymmetric, such as the back pressure on the opposite sides of the die of the stepped parting surface is not equal.
4动模板弯曲模具在注射时,模腔内熔融塑料产生巨大的反压力,一般在600~1000公斤/厘米。模具制造者有时不重视此问题,往往改变原设计尺寸,或者把动模板用低强度钢板代替,在用顶杆顶料的模具中,由于两侧座跨距大,造成注射时模板下弯。
4. When the movable template bending mold is injected, the molten plastic in the mold cavity produces a huge back pressure, generally 600 ~ 1000 kg / cm. Sometimes mold manufacturers do not pay attention to this problem, often change the original design size, or replace the moving template with low-strength steel plate. In the mold with ejector rod, the template is bent down during injection due to the large span of seats on both sides.
方法故动模板必须选用钢材,要有足够厚度,切不可用A3等低强度钢板,在必要时,应在动模板下方设置支撑柱或支撑块,以减小模板厚度,提高承载能力。
Solution: therefore, the moving formwork must be made of high-quality steel with sufficient thickness. A3 and other low-strength steel plates shall not be used. If necessary, support columns or blocks shall be set under the moving formwork to reduce the thickness of the formwork and improve the bearing capacity.
5顶杆弯曲,断裂或者漏料自制的顶杆质量较好,就是加工成本太高,现在一般都用标准件,质量要差一些。顶杆与孔的间隙如果太大,则出现漏料,但如果间隙太小,在注射时由于模温升高,顶杆膨胀而卡死。
5 the ejector rod is bent, broken or leaked. The self-made ejector rod is of good quality, but the processing cost is too high. Now standard parts are generally used, and the quality is worse. If the gap between the ejector rod and the hole is too large, there will be material leakage, but if the gap is too small, the ejector rod will expand and jam due to the increase of mold temperature during injection.
更危险的是,有时顶杆被顶出一般距离就顶不动而折断,结果在下一次合模时这段露出的顶杆不能复位而撞坏凹模。
What's more dangerous is that sometimes the ejector rod can't move and break when it is pushed out for a general distance. As a result, the exposed ejector rod can't be reset at the next mold closing, and the die is damaged.
方法为了这个问题,顶杆重新修磨,在顶杆前端保留10~15毫米的配合段,中间部分磨小0.2毫米。所有顶杆在装配后,都必须严格检查配合间隙,一般在0.05~0.08毫米内,要保证整个顶出机构能进退自如。
Solution: in order to solve this problem, the ejector rod shall be reground, the matching section of 10 ~ 15mm shall be reserved at the front end of the ejector rod, and the middle part shall be ground smaller by 0.2mm. After all ejector rods are assembled, the fit clearance must be strictly checked, generally within 0.05 ~ 0.08mm, to ensure that the whole ejector mechanism can move forward and backward freely.
6冷却不良或水道漏水模具的冷却效果直接影响制品的质量和生产效率,如冷却不良,制品收缩大,或收缩不均匀而出现翘面变形等缺陷。另一方面模整体或局部过热,使模具不能正常成型而停产,严重者使顶杆等活动件热胀卡死而损坏。
6 poor cooling or water leakage, the cooling effect of the mold directly affects the quality and production efficiency of the product, such as poor cooling, large shrinkage of the product, or uneven shrinkage and warping deformation. On the other hand, the overall or local overheating of the die makes the die unable to form normally and stop production. In serious cases, the movable parts such as the ejector rod are blocked by thermal expansion and damaged.
故障主要原因冷却系统的设计,加工以产品形状而定,不要因为模具结构复杂或加工困难而省去这个系统,特别是大中型模具一定要充分考虑冷却问题。
The main reason for the failure is that the design and processing of the cooling system depend on the product shape. Do not omit this system because of the complex die structure or difficult processing. In particular, the cooling problem must be fully considered for large and medium-sized dies.
7滑块倾斜,复位不顺有些模具因受模板面积限制,导槽长度太小,滑块在抽芯动作完毕后露出导槽外面,这样在抽芯后阶段和合模复位初阶段都容易造成滑块倾斜,特别是在合模时,滑块复位不顺,使滑块损伤,甚压弯破坏。
7. The slide block is inclined and the reset is not smooth. Due to the limitation of the template area, the length of the guide groove is too small, and the slide block is exposed outside the guide groove after the core pulling action is completed. In this way, the slide block is easy to be inclined in the post core pulling stage and the initial stage of mold closing reset, especially in the mold closing, the slide block is not reset smoothly, resulting in damage to the slide block or even bending damage.
方法根据经验,滑块完成抽芯动作后,留在滑槽内的长度不应小于导槽全长的2/3。
Solution according to experience, after the slider completes the core pulling action, the length left in the chute shall not be less than 2 / 3 of the total length of the guide groove.
8定距拉紧机构失灵摆钩、搭扣之类的定距拉紧机构一般用于定模抽芯或一些二次脱模的模具中,因这类机构在模具的两侧面成对设置,其动作要求必须同步,即合模同时搭扣,开模到一 定位置同时脱钩。一旦失去同步,势必造成被拉模具的模板歪斜而损坏,这些机构的零件要有较高的刚度和耐磨性,调整也很困难,机构寿命较短,尽量避免使用, 可以改用其他机构。
8. Fixed distance tensioning mechanism fails. Fixed distance tensioning mechanisms such as swing hook and buckle are generally used in fixed mold core pulling or some secondary demoulding molds. Because these mechanisms are set in pairs on both sides of the mold, their actions must be synchronized, that is, the mold is buckled at the same time, and the mold is decoupled at the same time when it is opened to a certain position. Once the synchronization is lost, it is bound to cause the formwork of the drawn die to be skewed and damaged. The parts of these mechanisms should have high stiffness and wear resistance. It is also difficult to adjust. The service life of the mechanism is short. Try to avoid using it and use other mechanisms instead.
故障主要原因斜销滑块式抽芯机构损坏这种较常出现的毛病大多是加工上不到位以及用料太小,主要有以下问题:
The main cause of the failure is the damage of the inclined pin sliding block core pulling mechanism. Most of the common problems are that the processing is not in place and the material is too small. The main problems are as follows:
斜销倾角A大,优点是可以在较短的开模行程内产生较大抽芯距。但是采取过大的倾角A,当抽拔力F为一定值时,在抽芯过程中斜销受到的弯曲力 P=F/COSA,也越大,易出现斜销变形和斜孔磨损。同时,斜销对滑块产生向上的推力N=FTGA也越大,此力使滑块对导槽内导向面的正压力增大,从而 增加了滑块滑动时的摩擦阻力。易造成滑动不顺,导槽磨损。根据经验,倾角A不应大于25。
The inclination angle a of the inclined pin is large, which has the advantage that it can produce a large core pulling distance in a short mold opening stroke. However, if the inclination angle a is too large, when the pulling force F is a certain value, the bending force P = f / cosa of the inclined pin in the core pulling process is also larger, which is prone to deformation of the inclined pin and wear of the inclined hole. At the same time, the upward thrust n = ftga generated by the inclined pin on the slider is also greater, which increases the positive pressure of the slider on the guide surface in the guide groove, thus increasing the friction resistance when the slider slides. It is easy to cause unsmooth sliding and wear of guide groove. According to experience, the inclination A shall not be greater than 25.
方法在抽心力比较小的情况下可采用弹簧推出定模的方法,在抽芯力比较大的情况下可采用动模后退时型芯滑动,先完成抽芯动作后再分模的结构,在大型模具上可采用液压油缸抽芯。
Solution: when the core pulling force is relatively small, the method of spring pushing out the fixed mold can be adopted. When the core pulling force is relatively large, the structure of core sliding when the moving mold retreats, first completing the core pulling action and then dividing the mold can be adopted. The core pulling of hydraulic cylinder can be adopted on large molds.
9注塑模具中排气不畅注塑模具中常常有气体产生,这是由什么产生的?
9. The exhaust in the injection mold is not smooth, and there is often gas in the injection mold. What is the reason for this?
故障主要原因浇注系统与模具型腔中存有的空气,有些原料含有没有被干燥排除的水分,它们在高温下会气化成水蒸气,由于在注塑时温度太高,某些性质不稳定的塑料会发生分解而产生气体;塑料原料中的某些添加剂挥发或者相互化学反应生成的气体。
The main reason for the failure is the air in the gating system and mold cavity. Some raw materials contain moisture that has not been dried out. They will be gasified into steam at high temperature. Due to the high temperature during injection molding, some unstable plastics will decompose and produce gas; Gases generated by volatilization or mutual chemical reaction of some additives in plastic raw materials.
同时排气不良不畅的缘由,也需要尽快找出来。注塑模的排气不良将会给塑件的质量等诸多方面带来一系列的危害,主要表现:在注塑过程中熔体将取代型腔中的气体,如果气体排出不及时将会造成熔体充填困难,导致注射量不足而不能充满型腔;排除不畅的气体会在型腔中形成高压,并且在一定的压缩程度下渗入塑料的内部,造成空洞、气孔、组织疏和银纹等质量缺陷。
At the same time, the cause of poor exhaust also needs to be found out as soon as possible. Poor exhaust of injection mold will bring a series of hazards to the quality of plastic parts and many other aspects, mainly as follows: in the injection process, the melt will replace the gas in the mold cavity. If the gas is not discharged in time, it will make it difficult to fill the melt, resulting in insufficient injection volume and unable to fill the mold cavity; Poor gas removal will form high pressure in the mold cavity and penetrate into the interior of the plastic under a certain degree of compression, resulting in quality defects such as cavities, pores, sparse tissue and crazing.
由于气体被高度压缩,使得型腔内温度急剧上升,进而引起周围熔体分解、烧灼,使塑件出现局部碳化和烧焦现象。它主要出现在两股熔体的合流处,浇口凸缘处;气体的排除不畅,使得进入各型腔的熔体速度不同,因此易形成流动痕和熔合痕,并使塑件的力学性能降低。由于型腔中气体的阻碍,会降低充模速度,影响成型周期,降低征税效率。
Because the gas is highly compressed, the temperature in the mold cavity rises sharply, which leads to the decomposition and burning of the surrounding melt, resulting in local carbonization and charring of the plastic parts. It mainly appears at the confluence of two melts, at the gate flange; The poor removal of gas makes the melt velocity entering each cavity different, so it is easy to form flow marks and fusion marks, and reduce the mechanical properties of plastic parts. Due to the obstruction of gas in the cavity, it will reduce the mold filling speed, affect the molding cycle and reduce the molding efficiency.
塑件中气泡的分布,模腔中积存空气所产生的气泡,常分布在与浇口相对的部位上;塑料原料中分解或化学反应产生的气泡则沿塑件的厚度分布;塑料原料中残存水气化产生的气泡,则不规则地分布在整个塑件上。
The distribution of bubbles in plastic parts. The bubbles generated by the accumulation of air in the mold cavity are often distributed on the part opposite to the gate; Bubbles produced by decomposition or chemical reaction in plastic raw materials are distributed along the thickness of plastic parts; The bubbles generated by residual water gasification in plastic raw materials are irregularly distributed on the whole plastic part.
Jinan injection mould http://www.sdlqmj.com/ Thank you for your browsing. If you have any other questions, please log in to our official website.